Top 5 Tips On Streamlining Your Garment Manufacturing Process
- adila82
- Jan 16, 2020
- 3 min read
Updated: Jun 19, 2024
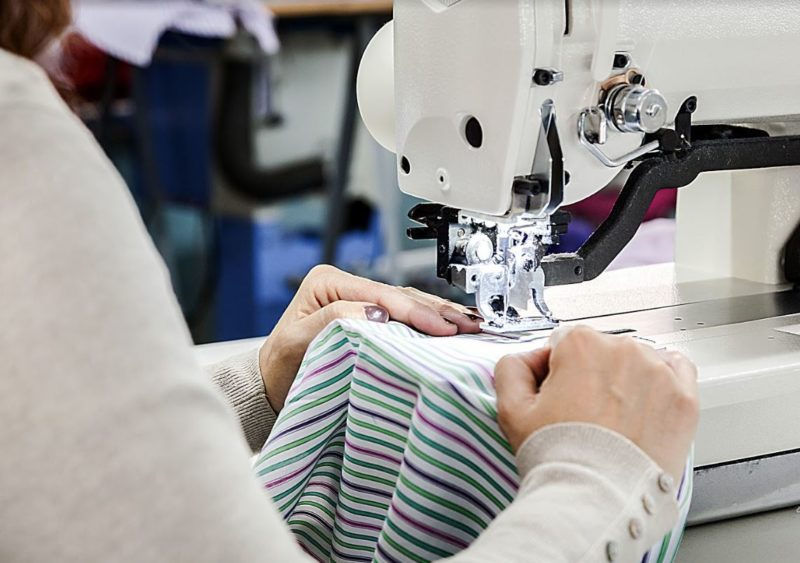
Sew – have you ever painted your nails and, as you’re about to finish the final coat, you ruin one nail so you have to start that nail all over again? This is what it will be like once you’ve started working with a manufacturer and production is underway but then, oops! – an issue pops up that costs you time and money. To prevent this, here’s a list of five most important things to take care of.
1. Schedule Each Step – Do it Smartly
(Aka calculate the overall time it takes for the pre-production process.)
Because initially, it takes time to fully understand the entire manufacturing process, a workback schedule is needed. This is a guide to help plan the amount of time needed to efficiently organize and manage tasks.
Be aware: If you have more than one delivery, and you need to work on different steps, creating a workback schedule can get tricky, just stay focused on each individual delivery timeline, and accurately estimate how long each step needs to take.
Tip: You may want the schedule to be tight, but do allow for a margin of error.
Your workback considerations:delivery date, ship dates, manufacturing time, pre-production and average lead-time from prototyping (the first sample created from your pattern).
Your mantra: Plan. Schedule. Be Flexible.
2. Design with costs in mind.
Simple designs cost less to manufacture; complex details cost more. Remember that!
This one is all about production/manufacturing costs and budgeting. Before you commit to a factory you need to know your desired selling point, target costs and estimated “mock” purchase order. Also, make sure the product and quantity you need lies within the scope of your factory. If you don’t provide your manufacturer with an estimated budget and target cost, the factory won’t know the quality standard to work within.
Your mantra: More is more. Less is less. And quality always matters.
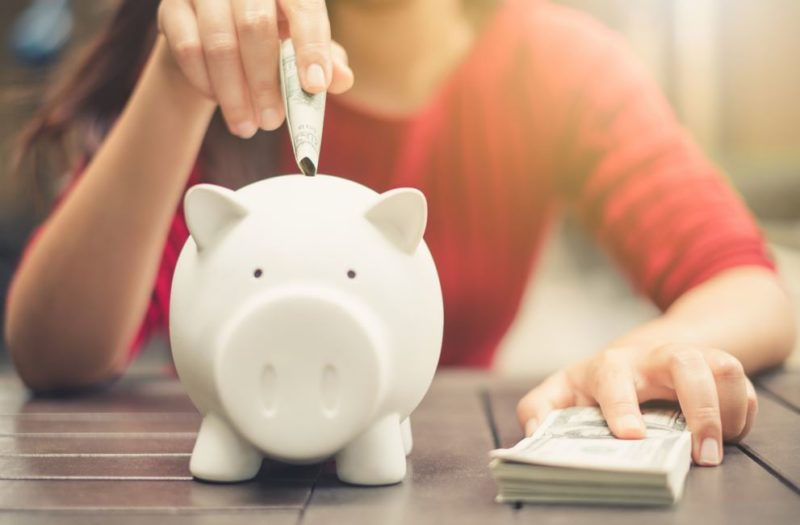
3. You need a tech pack.
A tech pack is a blueprint for your designs. You need a good one.
This “blueprint” is essentially a tell-all sketch of your design created by you to communicate to your manufacturer, every single detail needed to make your product – i.e.: measurements, fabric, color, trimming, tags, labels, etc.
Don’t stint on the details!! When your tech pack is thorough, you increase the chance of your chosen factory doing a stellar job. Sew – right upfront give the factory a “tell all” techpack so there’s no doubt of what you want. To help put together their tech pack, many brands and designers work specifically with technical designers.
Mantra: Don’t ditch the details.
4. Before you go overseas, go local!
The perfection of your prototype needs a local crew. Go for it.
The initial prototyping process/product development is important and is best done locally. To ensure your designs are 100% accurate, you’ll need face-to-face meetings and hands-on examination of your product.
Your ideal crew: a technical designer, a graphic designer, pattern makers, and sample makers. To save money, you might be inclined to do things on your own but don’t. This is an essential part of your production and it needs to be done properly. Once you sign off on the finished and perfected prototype you have something to forward to your manufacturer.
Mantra: Perfect prototypes yield the best results in production.
5. Fabric Facts
Easy to overlook, but knowing the composition of your fabric is essential.
Here’s something to remember: the more you know about the composition of your fabric, the better the outcome of your design will be. What’s the fabric weight, structure, and fiber content? Knowing the difference between woven and knit fabric and knowing how each responds to the manufacturing process is vital. Being familiar with every detail of your fabric – say needing to have an element of the design on the sleeve, will help you find a factory with the proper equipment and capabilities.
Mantra: Be a material girl – know your fabric.
Summing Up!
Sew – as you’ve read above, the pre-production process has several moving pieces and a lot of tasks to remember.
During this pre-production step of the 'product-to-market process', you’ll need to focus on the minutiae of production. It’s time when the research, design, finances, manufacturing factory, and the act of production itself have to work together in ways that result in a perfectly manufactured product that’s on time, on budget, and on its way to making you a profit.
Not sure how to get started? Check out the our manufacturing consultation, and get the industry secrets you need to get your brand started. Check it out here!
Comentarios